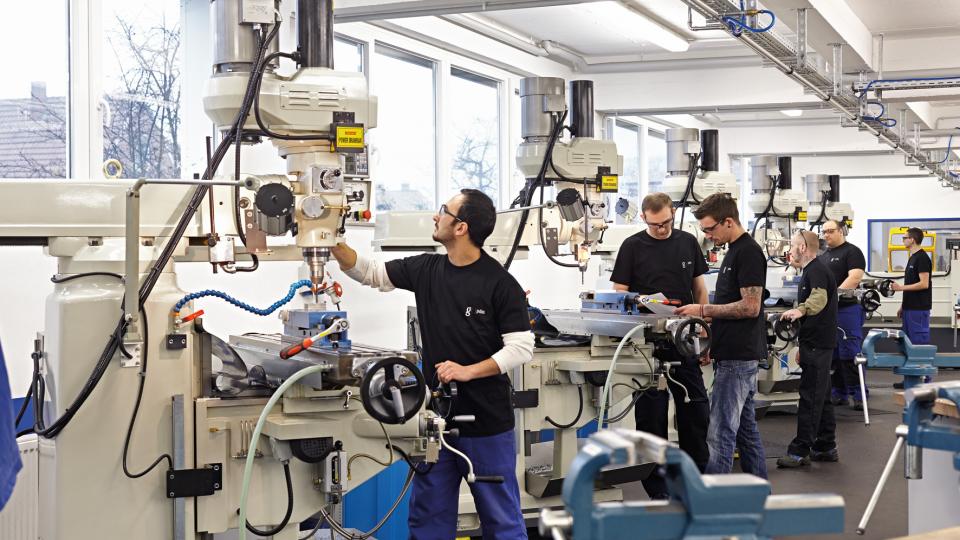
Wo Computer, Roboter und der Mensch kooperieren
Der Mitarbeiter, ganz in Orange, sucht offenbar nach seiner Bestform. Der Griff in die Ablage für Bretter gelingt ihm weniger geschmeidig als üblich. Beinahe verrutscht ein Brett, was zu einem Folgeproblem beim Anbringen der Scharniere führen könnte. So wird kein Schuh draus, besser gesagt: kein tauglicher Schaltschrank. Zugegeben, die nicht optimale Arbeit ist diesmal gewollt, sie dient Markus Kamann zu Demonstrationszwecken – an einem Mitarbeiter, der nicht aus Fleisch und Blut ist. „So läuft es ab, wenn jemand den Greifroboter nicht richtig programmiert“, sagt der Geschäftsführer der Gesellschaft für Projektierungs- und Dienstleistungsmanagement (gpdm) aus Paderborn. „Er ruckelt enorm und sein Greifer verliert mit Pech die Hälfte. Übernimmt ein Robotik-Fachmann das an meiner Stelle, läuft die Produktion natürlich fließend. Das Programmieren, aber auch die Fehleranalyse oder die Wartungstechnik bieten wir hier in Lehrgängen an.“
Hier, das ist das moderne Trainingszentrum Verl des „Beruflichen AusbildungsNetzwerks im Gewerbebereich“ (BANG). Hier hat Kamanns Gesellschaft gpdm mit Unternehmen der Region und der Unterstützung des Landes Nordrhein-Westfalen eine BANG-Lehrfabrik Industrielle Informatik installiert. Ihr Kern ist die 200 Quadratmeter umfassende Lehrinsel „Industrie 4.0“ mit dem orangefarbenen Industrieroboter. Um die Insel ist eine Grundlagenlehrwerkstatt für Mechatronik, Elektrotechnik, Informatik und Wartungstechnik angeordnet. Je nach Lehrgang und Berufsbild lässt sie sich passend ausstatten, mobile Container liefern entsprechendes Material, Werkzeuge und Projektaufgaben binnen kurzer Zeit aus den Lagerräumen. „Wegen dieser schnellen Wandelbarkeit bezeichnen wir Verl als MINT Industrie 4.0 Hybridzentrum“, sagt Markus Kamann. Damit ist eine Arbeitsumgebung entstanden, die computergestützte Produktionsprozesse mit Robotik verbindet und somit den Stand der Digitalisierung zeigt. Sie entspreche zudem der realen Arbeitswelt Metall verarbeitender Betriebe in Ostwestfalen/Lippe, betont Markus Kamann.
1,5 Millionen Euro für eine moderne Realanlage
Wo BANG eines seiner mittlerweile 15 Trainings- bzw. Ausbildungszentren unterhält, haben immer mindestens sechs bis zehn Firmen einer Branche sich zusammengetan. Sie wollen die Ausbildung junger Menschen und die Qualifizierung ihrer Beschäftigten gemeinsam auf hohem Niveau voranbringen – und das branchenspezifisch. Im Kreis Gütersloh etwa arbeitet BANG an inzwischen sogar zwei Standorten für 42 vernetzte Unternehmen aus den Bereichen Metall, Kunststoff, Elektro, Lebensmittel & Getränke sowie Blech. Mitte des Jahrzehnts erhält BANG den Zuschlag für ein Förderprojekt innerhalb des Fachkräfteaufrufs des Landesministeriums für Arbeit, Gesundheit und Soziales (MAGS), den Stand der Digitalisierung in der Metallverarbeitung mit einem modernen Maschinen- und Anlagenpark am Standort Verl abzubilden. Markus Kamanns Gesellschaft generiert über die Mittel aus dem Europäischen Fonds für regionale Entwicklung (EFRE) und dem Europäischen Sozialfonds (ESF) sowie Industriesponsoring insgesamt rund 1,5 Millionen Euro für Ausstattung, Lehrpersonal und Didaktik der Lehrfabrik Industrielle Informatik. Bis zu ihrem Start im Herbst 2017 hatte das Trainingszentrum Verl bereits in zwei Jahren 110 junge Menschen in der praktischen Ausbildung unterstützt. Sie stammten aus mehr als einem Dutzend Berufen der Metall- und Elektro-Branche und hatten bis dahin manuelles und maschinelles Spanen, Drehen, Fräsen, Pneumatik und Schweißtechnik gelernt. Hinzu gekommen sind durch die Millionen-Investition nun Lehrmodule für die Bereiche Montage, Elektrotechnik, Steuerungstechnik, Mechatronik und Robotik.
Warum aber nutzen über 40 Unternehmen der Region ein Angebot, das neben die Säulen des dualen Ausbildungssystems, Berufsschule und Betrieb, mit den BANG-Lehrfabriken noch eine dritte stellt? Die Antwort reicht bis in die 1990er-Jahre zurück. Trotz hoher Jugendarbeitslosigkeit hatten nicht wenige Technologie-Unternehmen aus der Region Hövelhof nördlich von Paderborn große Probleme, ihre freien Stellen zu besetzen. Herkömmliche Ideen für das Anwerben von Auszubildenden griffen nicht mehr. Der Mangel war vielfältig: Zu wenig Fachkräfte und nicht ausreichend Auszubildende einerseits. Andererseits dünnten in den Betrieben auch die Ressourcen unter den qualifizierten Ausbildenden oder beim adäquaten Maschinenpark aus. Die Agentur für Arbeit Paderborn und die Industrie- und Handelskammer (IHK) Bielefeld forcierten eine große Lösung, ein neuartiges Konzept für eine moderne und attraktive Ausbildung. Markus Kamanns Gesellschaft gpdm, eine Ausgründung der Universität Paderborn, erhielt den Auftrag. Sie entwickelte die Netzwerk-Idee für eine Ausbildung, die von verschiedenen Unternehmen einer Branche gemeinsam getragen wird. „Wir bieten den beteiligten Firmen alles, was sie besser in Kooperation erledigen lassen, um nicht unnötig Geld zu verbrennen“, sagt Markus Kamann.
Mitgliedsbeiträge, Lehrgangsgebühren und großzügige Spender
Der Vorteil für die mittelständischen Unternehmen liegt nicht allein darin, die eigenen Auszubildenden für eine bestimmte Anzahl an Tagen beziehungsweise Lehrgängen in eine moderne Ausbildungsumgebung zu schicken. BANG bietet mehr und setzt schon früher ein, bei der Berufsorientierung und der Bewerbervorauswahl. Junge Menschen können sich direkt bei BANG um einen Ausbildungsplatz bewerben und werden im Idealfall an eins der Netzwerk-Unternehmen vermittelt. Über die Ausbildung hinaus qualifiziert das Netzwerk auch Fachkräfte weiter. „BANG spricht mit seinen Angeboten elf verschiedene Zielgruppen an“, sagt Markus Kamann, „von Schülern und Auszubildenden über Fachkräfte und Langzeitarbeitslose bis hin zu Geflüchteten und Menschen, die in den Beruf zurückkehren möchten.“ Der Anspruch dabei sei es, „eine hochprofessionelle Ausbildungs-, Personalentwicklungs- und Weiterbildungsabteilung zu sein, wie man sie aus großen Unternehmen kennt. Allerdings mit einem auf Mittelständler zugeschnittenen Angebot“, sagt Markus Kamann.
Interessierte Unternehmen gründen unter dem BANG-Banner einen Verein, zahlen einen Mitgliedsbeitrag sowie spätere Teilnahmegebühren für die jeweiligen Module und Lehrgänge, die sie für ihre Auszubildenden oder Fachkräfte buchen. Das allein würde für die teils hohen Investitionen der Lehrfabriken nicht ausreichen. Daher wird Markus Kamann nicht selten bei Maschinenherstellern mit der Bitte vorstellig – er nennt es „Puderzucker verteilen“ –, großzügig bei der Ausstattung der Lernumgebungen zu helfen. So wie jüngst bei der vom Land geförderten Lehrfabrik für Blechbearbeitung in Steinhagen, die neben etlichen Zukäufen auch aus gesponserten Stanzen, Richtanlagen und Laserschneideanlagen besteht. Die Angebote dieser Trainingszentren und Lehrfabriken stehen selbst Firmen offen, die nicht zum Trägerkreis zählen. Inzwischen sind auf Initiative der gpdm auch außerhalb Nordrhein-Westfalens BANG-Netzwerke entstanden, darunter im niedersächsischen Bassum und im Nordschwarzwald.
Wenn Programme und Greifroboter einen Schrank bauen
Wie Computerprogramme und Robotertechnik miteinander funktionieren und welche Rolle dem Menschen in dem vernetzten Prozess zukommt, zeigt nun die Lehrinsel „Industrie 4.0“ in Verl. Ein kleiner Bereich der 200 Quadratmeter großen Fläche besteht aus Notebook-Arbeitsplätzen. Sie verfügen über Software, mit der Handwerker Schaltschränke, aber auch Endkunden Profanschränke konfigurieren und in Auftrag geben können. Nach dem Aktivieren des gewünschten Schrankmodells im Webshop landet die Bestellung in einem Manufacturing Execution System (MES), das den Herstellungsprozess an der nebenstehenden Produktionsstrecke automatisch anleitet. Alle folgenden Schritte sind digital aufeinander abgestimmt. Kommt ein Brett im Produktionsablauf zur Hochleistungsfräse, weiß diese, an welcher Stelle welche Art Loch zu bohren ist. Die Fräse identifiziert über einen Scanner, der den QR- oder Barcode am Brett ausliest, ob es sich um einen Deckel, Boden oder eine Seitenwand für den Schrank handelt. Mit den entsprechenden Bohrlöchern versehen, nimmt der orangene Greifroboter das Brett aus dem Schlitten und hält es vor eine Kamera. Hier erfolgt der Tauglichkeitstest. Über eine feine Punktwolke prüft das elektronische Auge bis zu 60.000 Einzelelemente, woraus sich die weitere Verwendung des Brettes ergibt. Sind die Bohrlöcher fehlerhaft, also zum Beispiel ausgefranst, landet es im Schredder. Ist alles in Ordnung, gibt der Roboter das Brett entweder in ein Fertiglager oder direkt in die weitere Verarbeitung. Beschläge und Scharniere kommen im nächsten Schritt hinzu.
Dies alles beschreibt Markus Kamann als „extrem verketteten Prozess“, der bei kleinsten Fehlern zum Erliegen komme. Etwa wenn der Roboter Bretter nicht greift und sich diese stapeln. Der Mensch kommt erst sichtbar ins Spiel, wenn es „nur noch“ um die verbleibende Montage der automatisch bearbeiteten Bretter geht. „In dieser kompletten Arbeitswelt sind die letzten Schrauben und das abschließende Zusammensetzen noch Handarbeit“, sagt Markus Kamann.
Aber auch am Rande der von Computern gesteuerten und von Robotern und Maschinen ausgeführten Produktion benötigt es Menschen mit besonderen Fähigkeiten. „Das Synchronisieren der gesamten Anlage über die Steuerungstechnik lernen unsere Auszubildenden und Fachkräfte hier.“ Neben den Steuerungstechnikern und Robotik-Programmierern rücken auch Wartungstechniker in den Vordergrund. Für sie gibt es spezielle BANG-Lehrgangsmodule über fünf Tage. „Betriebe brauchen die spezielle Qualifizierung von Menschen, die wissen, wie mehrere Millionen Euro teure Anlagen aufgebaut sind und wo sich Fehler verbergen können, wenn einmal eine ganze Produktionsstraße steht“, sagt Markus Kamann. Auch die Auszubildenden müssen bei BANG im dritten Lehrjahr nachweisen, dass sie die Aufgabe „Anlage läuft nicht“ auch ohne exakte Fehlerbeschreibung lösen können. „Die Fähigkeiten zur Fehleranalyse und das technische Wissen eignen sie sich idealerweise an Realanlagen wie unseren an“, sagt Markus Kamann.
Küchenbauer schickt Auszubildende im ersten Jahr komplett zu BANG
Realanlage ist ein Begriff, der in den Ausführungen Markus Kamanns besonderes Gewicht hat. Die „Lehrinsel Industrie 4.0“ sei insgesamt wie eine „kleine Fabrik“. Dass deren Systematik etwa beim Schrankbau „so nah an der Realität ist“, wie Markus Kamann sagt, ist kein Zufall. Sie ist angelehnt an die Produktionsstraßen von Nobilia, einem führenden Küchenhersteller mit Sitz in Verl und BANG-Netzwerkpartner, der über 3.000 Küchen am Tag produziert.
Wie Nobilia-Ausbildungsleiter Guido Krane erklärt, habe das Unternehmen lange überlegt, ein eigenes Ausbildungszentrum einzurichten, um den Bedarf an qualifizierten Mechatronikern für Betriebstechnik zu decken. „Ich bin eigentlich ein Anhänger der integrierten Ausbildung, damit die jungen Menschen direkten Kontakt zum Betrieb haben und alles sofort bis zur Instandhaltung kennenlernen“, sagt Guido Krane. Allerdings habe der Platz in der eigenen Werkstatt nicht ausgereicht, um den hohen Ansprüchen zu genügen. „Nach meiner Anfrage bei BANG haben wir dann in drei Meetings erarbeitet, wie mein Ausbildungskonzept in der Lehrfabrik umgesetzt werden könnte“, sagt Guido Krane. So starten die Mechatroniker-Auszubildenden von Nobilia – anfangs vier, inzwischen jährlich noch zwei – ihre Grundlagenausbildung in gesonderten Räumen bei BANG; sie verbringen dabei die kompletten 170 Praxistage des ersten Lehrjahrs dort. Erst im zweiten Jahr wechseln die Auszubildenden zu vertiefenden Projektarbeiten ins Werk, kehren aber auch für spezielle Module bis zum Ausbildungsende in die Lehrfabrik zurück. Nobilia hält über eine Teamentwicklungsfahrt vor Ausbildungsstart und eine große gemeinsame Projektarbeit im zweiten Lehrjahr den Kontakt zu seinen „ausgelagerten“ Auszubildenden. „Diese intensive Kooperation mit Nobilia ist eine besondere Ausnahme“, sagt Markus Kamann. Für gewöhnlich schicken Firmen ihre Auszubildenden für bestimmte Lernmodule zu BANG, die sie nicht im eigenen Betrieb anbieten wollen oder können.
Grundsätzlich empfindet Markus Kamann die Idee der BANG-Netzwerke nicht als Absage an die traditionell organisierte Ausbildung, sondern als Ergänzung, als „Add on“ mit etwa 60 Dienstleistungsbausteinen, zu denen auch spezielle Workshops für Ausbildende selbst zählen. „Ich bin ein Verfechter des dualen Systems, wir arbeiten hervorragend mit den Berufsschulen und Kollegs zusammen“, sagt er. Zudem kooperiert BANG in den Netzwerken mit Bildungsträgern, um zum Beispiel die Lehrerausbildung zu koordinieren und auf einem modernen Standard zu halten. „Aber es gibt Notwendigkeiten, das duale System anzupassen und zu modernisieren.“ Vier Punkte sind dabei für ihn wesentlich. Durch die fortschreitende Modernisierung und Digitalisierung industrieller Produktionsprozesse müsse erstens die betriebliche Realität viel stärker und deckungsgleich abgebildet werden, als es vielen Berufsschulen möglich sei. „Ich will die Realumgebung, nicht die Systeme, die Berufsschulen oft anschaffen.“ Dazu seien zweitens die BANG-Lerngruppen klein, sodass Auszubildende viel individueller gefördert werden könnten als in einem Klassenverband. „Das ist für die Betriebe zwar teurer, dafür aber effizienter“, sagt Markus Kamann. Als dritten Vorteil nennt er die gute Personalausstattung der BANG-Lehrfabriken, in denen Ingenieure, Meister und Betriebswirte im Verbund anleiten. Und schließlich erlebe er häufig an Berufskollegs das asynchrone Phänomen, dass es entweder ausreichend und gut qualifizierte Lehrende gebe, aber keine modernen Maschinen – oder umgekehrt eine gute Ausstattung, jedoch nicht die adäquaten Ausbildenden. Ihre Ausstattung hätten die Kollegs nicht selbst in der Hand, sie hänge von den öffentlichen Geldgebern, also zum Beispiel den Landkreisen ab. „Hier entscheidet sich die Frage, wie viel berufliche Bildung den Verantwortlichen wert ist“, sagt Markus Kamann.
Die BANG-Unternehmen lassen sich die Ausstattung ihrer Lehrfabriken durch ihre Beiträge etwas kosten. „Es ist eine aufwändige Arbeit, eine Lehrfabrik zu konzipieren, zu betreiben und auf dem neuesten Stand halten“, sagt Markus Kamann. Auf der Personalseite benötige es neben den Lehrenden jemanden, der den didaktischen Ansatz festlege und dazu die Vernetzung mit den Berufsschulen im Blick behalte. „Wir müssen immer die Brücke von den externen Ausbildungsinhalten zu dieser Insel bauen.“
In Köln entsteht eine Lehrfabrik zur Mensch-Maschine-Interaktion.
Wenn Firmen sich zu einem Netzwerk für gemeinsame Aus- und Fortbildung verbinden, dann aus gewichtigen Gründen. Das hohe Maß an Spezialisierung des Betriebes oder eine gute Auftragslage erlaubt es Firmen nicht immer, die eigenen Mitarbeiterinnen und Mitarbeiter und Auszubildenden in den eigenen Produktionsstätten angemessen zu qualifizieren. „Inzwischen vermitteln wir in allen technischen Berufen Auszubildenden die nötigen Zusatzerfahrungen“, sagt Markus Kamann. Nun ist es nicht die Regel, dass wie im Fall des Verler Küchenherstellers Auszubildende gleich sämtliche Praxistage im ersten Lehrjahr bei BANG verbringen. Für gewöhnlich, rechnet Markus Kamann vor, kämen die Auszubildenden neben den etwa 50 Tagen an ihrer Berufsschule im ersten Lehrjahr rund 60 Tage in eine BANG-Lehrfabrik. Die verbleibenden 110 Tage seien sie im Ausbildungsbetrieb. In den beiden weiteren Lehrjahren kämen Auszubildende in der Regel auf 50 beziehungsweise 20 BANG-Tage.
Das System der Ausbildungs-Netzwerke wächst weiter, die Digitalisierung ist ein wichtiger Aspekt. So entsteht in Köln federführend durch das Berufsförderungswerk (BFW) und die Diakonie eine Lehrfabrik zur Interaktion von Mensch und Maschine.
Auf 300 Quadratmetern konzipieren die Beteiligten den Bau idealtypischer Automaten. Auf den ersten Blick können sie unterschiedlicher nicht sein: Geld-, Park- und Kaffeeautomaten, Check-in-Geräte in Hotels oder Automaten der Verpackungsindustrie. Gemeinsam ist ihnen, dass Menschen sich an ihnen authentifizieren können oder müssen, zum Beispiel für den bargeldlosen Bezahlvorgang. Am Aufbau dieser Automaten, sozusagen an „lebenden Explosionszeichnungen“ (Markus Kamann), sollen Menschen aus acht verschiedenen Berufsfeldern lernen, darunter Mechatroniker, technische Produktdesigner, Geräte- und Systemelektroniker bis hin zu Zerspanungsmechanikern. „Uns umgibt eine Vielzahl von Automaten, und es werden immer mehr und immer komplexere“, sagt Markus Kamann. Daher eigne sich die Kölner Lehrfabrik auch für die Qualifizierung von Automatenfachmännern und -frauen, ein in Deutschland anerkannter Ausbildungsberuf. Wenn es um weitere Ziele geht, wendet Markus Kamann den Blick noch einmal nach Ostwestfalen/Lippe, einem wichtigen Standort der deutschen Möbelindustrie: „Sie täte gut daran, die Digitalisierung über die Auszubildenden und Mitarbeitenden in die eigenen Betriebe zu holen und die Belegschaften bei der Automatisierung stärker mitzunehmen.“ Er wüsste auch wie: durch eine auf die spezifischen Bedarfe der Möbelindustrie ausgerichtete BANG-Lehrfabrik.
Autor: Volker Stephan
Quelle: Dieser Text ist zuerst erschienen im G.I.B. Info 3/2019.
Social Media Einstellungen
Wenn Sie diese Felder durch einen Klick aktivieren, werden Informationen an Facebook, Twitter, Youtube, Google, Pinterest, Instagram, Flickr oder Vimeo übertragen und unter Umständen auch dort gespeichert.
Please note our notes and information on Privacy and for Netiquette, before you activate individual social media.
Permanently enable data feeds from social networks and agree to data transfer: