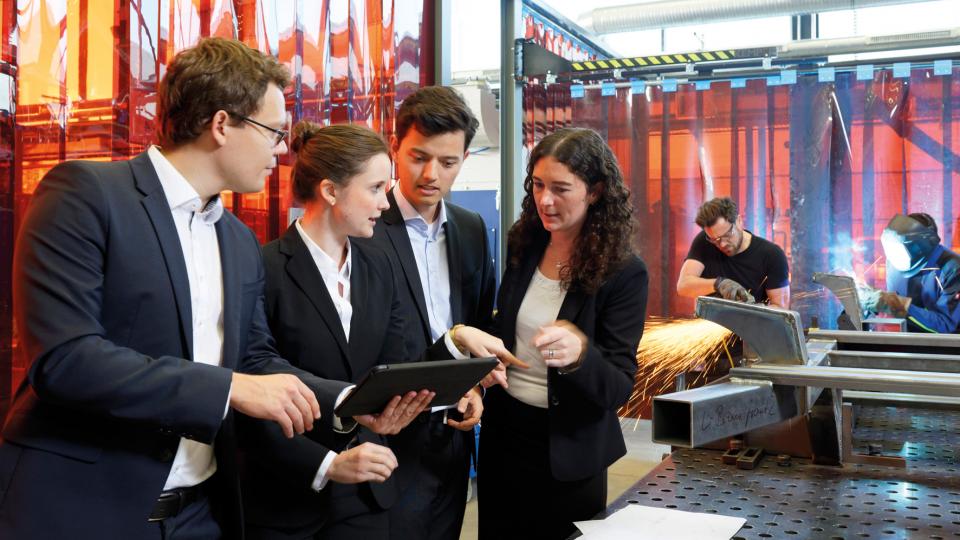
Industrie 4.0 smart organisieren mit der RWTH Aachen
Unter der Leitung der Abteilung Produktionsmanagement des Werkzeugmaschinenlabors WZL der RWTH Aachen, in Zusammenarbeit mit der Deutschen MTM-Vereinigung e. V. verfolgt das Projekt das Ziel, auch kleine Unternehmen in die Lage zu versetzen, die Möglichkeiten von Industrie 4.0 auszuschöpfen. Das vom Bund mit ESF-Mitteln für einen Zeitraum von drei Jahren finanzierte Vorhaben findet im Rahmen der „Initiative Neue Qualität der Arbeit (INQA)“ statt, die vom Bundesministerium für Arbeit und Soziales ins Leben gerufen wurde.
Die Projektidee entstand am WZL der RWTH Aachen. „Wir sind ein technisches Institut, das viel mit Beratungen zu tun hat, in deren Rahmen wir versuchen, Unternehmen – im Allgemeinen größere Mittelstandsunternehmen und Großunternehmen – voranzubringen“, erklärt Julian Ays, Projektverantwortlicher beim WZL. „Besonders das Thema Digitalisierung treibt uns dabei in den letzten Jahren natürlich um. Wir haben in dem Zusammenhang festgestellt, dass kleine Unternehmen auf diesem Feld allein schon wegen der Ressourcenfrage teilweise relativ stark gehemmt sind. Daraus ist die Idee entstanden, uns im Rahmen eines Projekts auf diese Unternehmen zu fokussieren.“ Weil auch der Faktor Mensch im Projekt eine wesentliche Rolle spielen sollte, wurde die für die Gestaltung produktiver und gesunder Arbeit bekannte Unternehmensvereinigung MTM, die ihre Expertise auf dem Gebiet der Arbeitswissenschaft und Arbeitspsychologie in das Projekt einbringt, als Kooperationspartner ins Boot geholt.Gemeinsam wurde überlegt, wie man kleineren und mittleren Unternehmen auf dem Weg in die Digitalisierung weiterhelfen könnte. „Es ging darum herauszufinden, wie die Mischung aus technischer Lösung und gleichzeitiger Qualifizierung der Mitarbeiter für diese Unternehmen aussehen muss“, so Julian Ays, „denn vor allem die Mitarbeiter sind das Kapital, auf das kleine und mittlere Unternehmen bauen.“ Dr. Thomas Mühlbradt vom Institut der Deutschen MTM-Vereinigung e. V. in Aachen und Mitglied im Projektteam ergänzt: „Uns geht es darum, die Begleitung der Unternehmen in Richtung Industrie 4.0 möglichst intelligent zu organisieren, sodass sie nicht überfordert sind.“ Ende 2016 startete das Projekt offiziell. Fünf Unternehmen mit zehn bis 100 Mitarbeiterinnen und Mitarbeitern entschlossen sich zur Teilnahme. Im Einzelnen sind dies die Polierscheibenfabrik G. A. Spaeth eK und der Maschinenbauer Ph-MECHANIK GmbH & Co. KG, beide in Aachen ansässig, die Periplast GmbH & Co. KG, ein Hersteller von Kunststoffprodukten mit Sitz in Wuppertal, die Julius Montz GmbH, ein Anlagenbauer für die chemische Industrie aus Hilden sowie die Rhein-Getriebe GmbH, die an ihrem Standort in Meerbusch Spezialgetriebe herstellt.„Wir haben festgestellt, dass die unternehmerische Bereitschaft, an einem solchen Projekt teilzunehmen, sehr unterschiedlich und stark von den verantwortlichen Personen abhängig ist“, stellt Julian Ays fest. Die Entscheidung in kleinen Unternehmen liege oft allein in der Hand des Geschäftsführers. Es gebe dementsprechend Unternehmen, die überhaupt kein Interesse zeigen, weil sie – so das Hauptargument – genug mit dem operativen Geschäft zu tun haben. Und es gebe die, bei denen sich der Geschäftsführer schon länger mit dem Thema beschäftige. „Die wollen sich sattelfest für die Zukunft machen, wissen aber nicht genau wie.“ Solche Geschäftsführer finden sich übrigens nicht nur im Projekt KMU 4.0. Auf dem Campus der RWTH Aachen können sich Unternehmen immatrikulieren und für eine gewisse Zeit in einem Büro einmieten, um sich so zum Beispiel für einen Tag pro Woche an verschiedenen Forschungsprojekten beteiligen zu können. Das nehmen einige Geschäftsführer kleinerer Unternehmen gerne wahr, in denen sich aus Ressourcen-Gründen nicht eigene Abteilungen mit der Digitalisierung auseinandersetzen können.
Lernprojekte als Kernelement
Im Rahmen des Projekts KMU 4.0 entwickelte das Projektteam gemeinsam mit den Unternehmen zum einen Ideen und digitale Lösungen für reale Probleme in Form von Lernprojekten, die das Kernelement des Projekts darstellen. Zum anderen wurden den teilnehmenden Unternehmen parallel Schulungen oder Workshops zu bestimmten Themen im Bereich Industrie 4.0 angeboten. Denn die Unternehmen müssen nicht nur die technischen Anforderungen im Bereich Sensorik, Virtualisierung und Vernetzung abdecken, sie haben auch die Veränderungen der Arbeitswelt zu berücksichtigen. Daraus resultiert ein doppelter Qualifizierungsbedarf für Unternehmen: Sie müssen sowohl technische Innovationen als auch Anforderungen an das Personalmanagement verstehen und umsetzen, sodass sie den Industrie-4.0-Trend in ihren Unternehmen gezielt mitgestalten können. Am Anfang eines Lernprojekts stand stets eine Analyse des Unternehmens, bei der der Status quo festgestellt wurde. Dabei wurden Schwachstellen ermittelt und im Anschluss technische oder organisatorische Optimierungsvorschläge erarbeitet. Wichtiges Element war dabei die intensive Einbindung der Mitarbeitenden in die Projekte. Von der Ermittlung von Schwachstellen über Verbesserungsvorschläge bis hin zum Testen von Lösungsvorschlägen waren sie beteiligt. Zur Mitarbeitereinbindung gehörten auch Besuche in der Demonstrationsfabrik Aachen, die eng verbunden ist mit dem WZL der RWTH Aachen. „Ein teilnehmendes Unternehmen kam sogar mit fast der kompletten Belegschaft zu uns. Der Geschäftsführer wollte einfach dafür sensibilisieren, in welche Richtung die Entwicklung des Unternehmens gehen kann“, verdeutlicht Julian Ays. In der Demonstrationsfabrik geht es nicht um eine reine Prototypendarstellung, es wird dort tatsächlich produziert. Den Besuchern im Rahmen von KMU 4.0 wurde dort in Form von Lernspielen vermittelt, warum die jeweilige technische Lösung einen Fortschritt bringt. Sie konnten selbst ausprobieren, ob sie im eigenen Arbeitsalltag sinnvoll einsetzbar wäre – ein weiteres wichtiges Element in dem Projekt-Konzept. Denn: „Das Problem ist aus unserer Sicht oft nicht, dass die technischen Lösungen zu teuer oder schwierig umzusetzen sind – es gibt oft Vorbehalte dagegen, weil man sich nicht vorstellen kann, was sie im Alltag wirklich bringen“, so Julian Ays. Auch Ängste der Mitarbeiter, dass man durch ein digitales System ersetzt werden könnte, könnten durch dieses Vorgehen abgebaut werden. Es gehe nicht darum, Arbeitskräfte zu ersetzen, sondern sie zu befähigen, digitale Systeme zu beherrschen. „Der wichtige Unterschied zu anderen Forschungsprojekten ist, dass die Mitarbeiter so qualifiziert werden, dass sie zukünftig selbst Entwicklungsprozesse in Richtung Industrie 4.0 durchführen können“, sagt Julian Ays.Dass das Konzept des Projekts KMU 4.0 greift, lässt sich etwa am Beispiel des kleinsten Unternehmens im Projekt zeigen, der Polierscheibenfabrik G. A. Spaeth, ein sehr traditionsreiches Unternehmen mit gerade einmal zehn Mitarbeitenden, das Polierscheiben aus gewebter Baumwolle herstellt. Überall, wo glänzende Oberflächen gefragt sind, werden diese Polierscheiben eingesetzt, zum Beispiel in der Autoindustrie. Sie werden sehr traditionell produziert, mit älteren Industrie-Nähmaschinen. In diese Maschinen müssen auf sehr komplizierte Weise Fäden eingefädelt werden. Der Inhaber führt die Einweisungen der Mitarbeitenden an diesen Maschinen oft selbst durch, was sehr zeitaufwändig ist. Deshalb suchte er nach Möglichkeiten, die ihm diese Aufgabe erleichtern könnten. Im Rahmen des Projekts kam man auf die Idee, den Optimalablauf des Arbeitsvorgangs in kleinen digitalen Clips aufzunehmen und diese dann an Tablets an dem jeweiligen Arbeitsplatz bereitzustellen. Mithilfe dieser „digitalen Unterweisungsbibliothek“ konnte die Einweisung von Mitarbeitenden an Maschinen vereinfacht und standardisiert werden. Außerdem wird so die Unterweisungsqualität dauerhaft gesteigert und die Dokumentation von betrieblichem Wissen sichergestellt. Die Einweisung funktioniert schneller und es passieren weniger Fehler. Das System wurde binnen weniger Monate entwickelt, getestet und implementiert. Die Polierscheibenfabrik Spaeth hat es so als kleinstes Unternehmen im Projekt am schnellsten geschafft ein funktionierendes neues digitales Hilfssystem einzuführen. Für Julian Ays ein gutes Beispiel, dass so etwas in kleinen Unternehmen möglich ist, wenn nur die Geschäftsführung und die Mitarbeiterschaft den Willen zeigen, in die Digitalisierung einzusteigen. Konzeptionell bewegt sich das Projekt KMU 4.0 im Rahmen der „Knowledge Triangel“. Das ist ein Rahmenkonzept der EU, das die drei Bereiche Forschung, Bildung und Innovation in Bezug setzt. Wobei der Aspekt Bildung seinen Platz als organisiertes Lernen in Form von Schulungen oder Workshops parallel zu den Lernprojekten hat. Allerdings kamen nicht alle Themen, die das Projekt-Team als für die KMU wichtig ansah, gleich gut bei den teilnehmenden Unternehmen an. Eine 40-stündige Schulung für die Geschäftsführungsebene, die der Orientierung auf dem Feld von Industrie 4.0 dient, nahmen die Beteiligten noch gerne mit. Andere Angebote zum Beispiel zum Thema Data-Analytics seien aber nicht angenommen worden, so Dr. Thomas Mühlbradt. So etwas werde als „Vorrats-Beschulung“ angesehen. Das sei aber schlicht nicht die Art, wie diese kleinen und mittleren Unternehmen arbeiten. „Erst wenn bestimmte Fragestellungen tatsächlich entstehen, schauen sie, wie sie sie bewältigen können. Man kann sagen, das ist strategisch nicht klug, aber es ist eine pragmatische Herangehensweise, die nüchtern auf die vorhandenen Ressourcen schaut.“Überhaupt wurde im Verlauf des Projekts festgestellt, dass die Gewichtung der Lernprozesse in der Realität anders war, als anfangs gedacht. So zeigte sich etwa, dass die überbetrieblichen Treffen im Rahmen des Projektes anders als von den Projektverantwortlichen erwartet immer sehr gut besucht waren. Es gibt also ein großes Bedürfnis nach wechselseitigem Austausch bei den KMU.
Vorurteile abgebaut
Neben dieser Erkenntnis und den konkreten Ergebnissen in den einzelnen Unternehmen konnte das Projekt KMU 4.0 auch mit bestimmten Vorurteilen aufräumen. Bei der Julius Montz GmbH zum Beispiel war der Führungsebene bewusst, dass seit dem letzten größeren Innovationsschub in dem Unternehmen schon einige Jahre ins Land gegangen waren. Sie zögerte aber, den Schritt in Richtung Digitalisierung zu gehen, weil man befürchtete, dass viele ältere Mitarbeitende diesen Schritt nicht mitgehen würden. Bei der Befragung der Mitarbeitenden im Workshop zeigte sich genau das umgekehrte Bild. Ihnen war durchaus bewusst, dass viele Dinge, zum Beispiel Laufmappen, mit denen die Aufträge begleitet werden, heute völlig anachronistisch sind. Allerdings vermutete die Belegschaft, dass die langjährige Geschäftsführung einen digitalen Wandel nicht mehr mittragen würde. „Beide Seiten haben im Rahmen von KMU 4.0 erkannt, dass ihre Positionen so nicht stimmen“, sagt Dr. Thomas Mühlbradt. „Das mündete dann in eine konkrete Tool-Entwicklung für die Produktionsplanung.“
Kleine Lösungen als Einstieg
Hat das Projekt Erkenntnisse darüber gebracht, was KMU generell fehlt auf dem Weg zur Industrie 4.0? „Bei kleineren Unternehmen sind fehlende Software oder lückenhafte Datenbestände anders als bei Großunternehmen nicht das größte Problem“, sagt Julian Ays. Das ließe sich meistens noch ändern. In den meisten Fällen fehle aber der Wille zur Veränderung und die Bereitschaft, sich ernsthaft mit der Digitalisierung auseinanderzusetzen. Auf der anderen Seite sieht das Projektteam gerade bei kleineren Unternehmen ein großes Potenzial zur Veränderung, die zum Teil mit einfachen Mitteln erreichbar ist, wie das Beispiel der Polierscheibenfabrik Spaeth zeigt. Dabei braucht es oft keine „große“ Lösung, etwa ein ERP-, MES- oder PLM-System1. Die Komplexität solcher Systeme sei oft erschlagend, sagt Julian Ays. „Das meiste, was in diesen Programmen an Potenzial drinsteckt, kann gar nicht abgerufen werden und die nötige Qualifizierung ist im Klein- und Mittelstand oft auch nicht vorhanden.“ Im Projekt KMU 4.0 war der Ansatz von daher eher der, kleine Tools zu programmieren, die ein konkretes Problem lösen. Diese Tools basieren zum Beispiel auf Access, einer Anwendung innerhalb des Microsoft-Office-Pakets. Es ist nicht aufwändig, dieses Programm umzuprogrammieren, die Benutzungsoberfläche kann leicht angepasst werden, die Benutzung ist für den Anwender, der in der Microsoft-Welt unterwegs ist, relativ intuitiv, und es stößt bei den Unternehmen auch auf mehr Akzeptanz, wenn sie sich nicht durch ein äußerst umfangreiches System kämpfen müssen, von dessen Funktionen sie nur einen Bruchteil nutzen. „Wir wissen natürlich, dass es nicht die perfekte Lösung ist, viele einzelne Tools zu entwickeln, weil es ja heute um Vernetzung geht“, sagt Julian Ays. „Aber es kann ein erster Schritt sein. Wenn ein Unternehmen dann den nächsten Schritt zu einem großen System macht, kann es deutlich kompetenter die eigenen Anforderungen formulieren, und das passende System auswählen.“Das Projekt KMU 4.0 läuft noch bis Ende September 2019. Die Erkenntnisse aus dem Projekt werden in der verbleibenden Zeit in einem Qualifizierungskonzept für kleine und mittlere Unternehmen zusammengefasst und in einer Leitbroschüre veröffentlicht. „Allerdings haben wir die Erfahrung gemacht, dass das zu wenig ist“, sagt Julian Ays. „Jedes Forschungsprojekt produziert eine neue Broschüre, die von weniger Menschen gelesen wird, als man sich das wünschen würde, – und was am Ende davon umgesetzt wird, ist fraglich.“ Im Moment verhandeln die Projektträger deshalb mit dem Bundesarbeitsministerium über eine einjährige Verlängerung des Projekts. Die Zeit soll genutzt werden, um in einen deutlich breiteren Transfer einzutreten. Geplant sind dazu Info- und Qualifizierungs-Veranstaltungen, idealerweise unter Beteiligung der Projekt-Unternehmen. Auch eine mediale Verbreitung der Erkenntnisse aus dem Projekt und Kooperationen mit Multiplikatoren wie Verbänden oder IHKs sind angedacht. „Das“, so Julian Ays, „ist aus unserer Sicht ein Weg, deutlich mehr interessierte Unternehmen zu erreichen und den Transfer durch den persönlichen Kontakt nachhaltiger zu gestalten.“
Autor: Frank Stefan Krupop
Quelle:Dieser Text ist zuerst erschienen im G.I.B. Info 3/2019.
Social Media Einstellungen
Wenn Sie diese Felder durch einen Klick aktivieren, werden Informationen an Facebook, Twitter, Youtube, Google, Pinterest, Instagram, Flickr oder Vimeo übertragen und unter Umständen auch dort gespeichert.
Please note our notes and information on Privacy and for Netiquette, before you activate individual social media.
Permanently enable data feeds from social networks and agree to data transfer: